NEWS
NEWS FROM CORETH
Certified products with PCR & PIR recyclate!
A large number of products with PIR/post industrial recyclate and PCR/post consumer recyclate content have been successfully certified externally by DIN CERTCO. We will be pleased to inform you.
New filter in the recycling process
The new melt filter promises higher quality of regranulate in CORETH's own recycling center! The innovative melt filtration technology, which filters impurities from contaminated plastics in high percentages and down to an impurity size of only 100 micrometers, improves the quality of the regranulate. Even films with paper labels can thus be sent to our recycling plant without any problems!
We are also happy to take on your contract recycling orders!
Translated with www.DeepL.com/Translator (free version)
Expansion of raw material silos
In order to be able to ensure the raw material supply also in the future, the company Coreth extends its silos by further 4 silos à 180 sqm³.
In addition, all day silos and the complete infrastructure will be renewed.
No dependence on natural gas!
Coreth's extrusion and conversion lines are not operated with natural gas or crude oil.
Long-term electricity contracts ensure the manufacturing capacity of our company!
Film with high regenerate content!
Together with our German cooperation partner, we have developed a film with a regenerate content of 94%, which has been certified by TÜV Rheinland!
The high regenerate content of 94% is obtained from our own recycling center at the company site!
Successful completion of the "Packloop" project!
In this exciting project, the use of post-consumer recylate in secondary packaging was analyzed in detail at CORETH. The results of this study provide an important contribution for future developments and implementations to achieve the challenging goals of the EU Circular Economy Package and for the necessary use of recyclates.
Further details can be found in our "Green Zone".
Coreth now stacks electrically with Jungheinrich!
We are replacing our diesel forklift fleet with environmentally friendly and high-performance electric forklifts from Jungheinrich, our long-standing partner for forklifts and warehouse systems.
More ecological, accessible and with reduced noise
The vehicles not only offer a better eco-balance, but also lower maintenance requirements and higher accessibility. In addition, they operate remarkably quietly.
And the new electric forklifts run on green energy from our own PV system!
This project is particularly focused on innovation and sustainability.
Installation of a photovoltaic system!
In collaboration with VERBUND Energy4Business GmbH, we have built a 170 kWp photovoltaic system as a self-consumption model in three of our production halls. The production of solar energy is highly advantageous as the PV company model by VERBUND guarantees a risk-free installation without the initial investment costs. All of the energy generated by the sun flows directly into our production cycle. This enables us to save on energy costs and increase our energy independence, reaching our goal of reducing CO2 emissions by up to 13 tons per year.
copyright "@VERBUND"
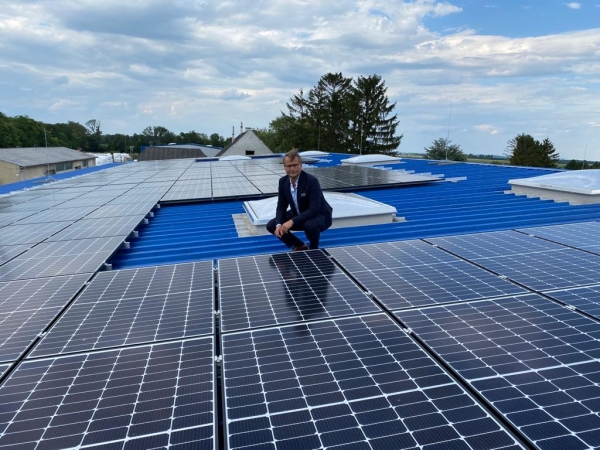
Latest generation of the Varex 2 now on operation!
After a successful partial increase of the production hall, the latest generation of the Varex 2 from W & H was put into operation. In addition to a significantly higher production output, this new extruder gives us more flexibility in production planning.
We have been successfully re-certified according to the EN 15593 hygiene quality standards!
We are expanding our printing hall and building a high-rise warehouse!
We are increasing our printing hall by 1.200 square metres to accomodate a hygienic HACCP high-rise warehouse and are optimising our storage concept for semi-finished and finished goods.
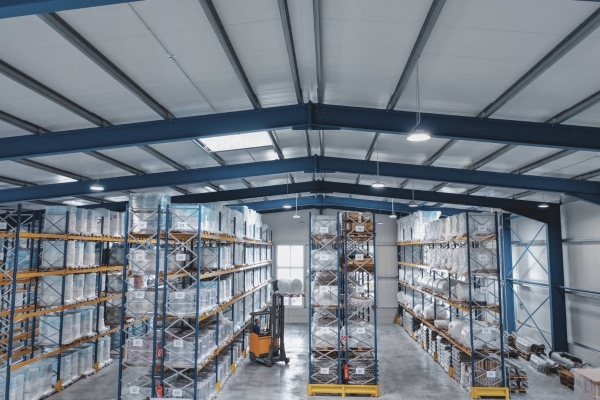
We are increasing our energy efficiency by 7,7% and demonstrably reducing our CO2 emissions by 7,9%!
As part of the ECO-NET energy efficiency network, we received an award for our valuable contribution to protecting our energy resources!
Second Varex 2 blown film system
We have commissioned another Varex 2 blown film system from Windmöller & Hölscher, specialised for the manufacturing of stretch tubing!
Certificate EN 15593
We received the EN 15593 Certificate!
This certification guarantees a complete management system for the production in the packaging for foodstuffs.
Coreth is a member of respACT!
We are affiliated with Austria´s leading platform for CSR (Corporate Social Responsibility) for responsible business management.
Our focus is now centred on reaching our economic, ecological and social goals. We strive to operate responsibly in the market and towards employees, society and the environment.
State-of-the-art blown film extruder by Windmöller & Hölscher (Varex 2)
Start-up of the new blown film extruder with a maximum output of 800 kg/h.
The extruder of the latest series by the German premium supplier is the first of its kind installed in Austria!
Max. working width: 2,800 mm; max. film width: 3,200 mm
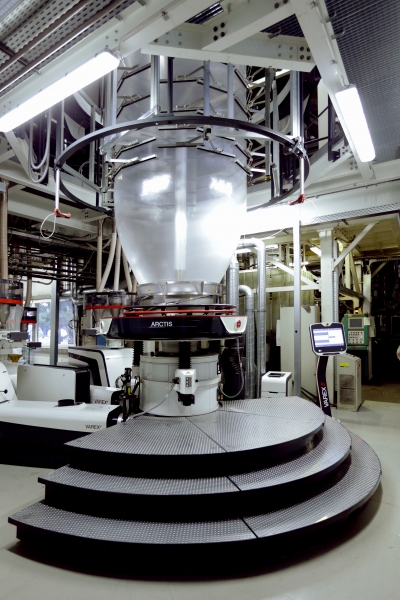
Partial increase of production hall height to 19.5 metres
In order to ensure maximum output of the new extruder and a consistently high film quality, the height of the production hall was increased in some parts to 19.5 metres in May 2014!
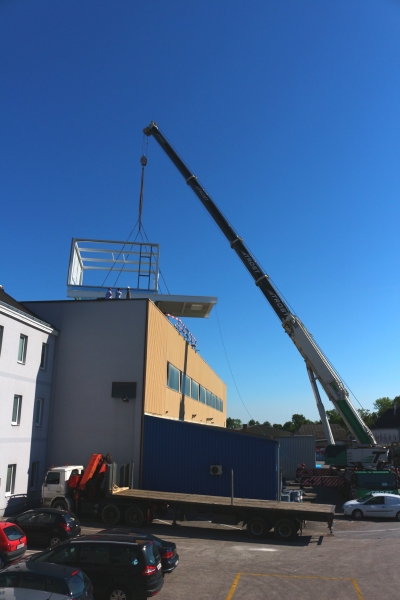
Distinguished as a leading company by Leitbetriebe Austria again!
Leitbetriebe Austria is an independent economic network that distinguishes exemplary companies in Austria.
Sustainable corporate success, innovation and social accountability are the factors primarily focused upon during the certification process.
We will be pleased to give you more detailed information!
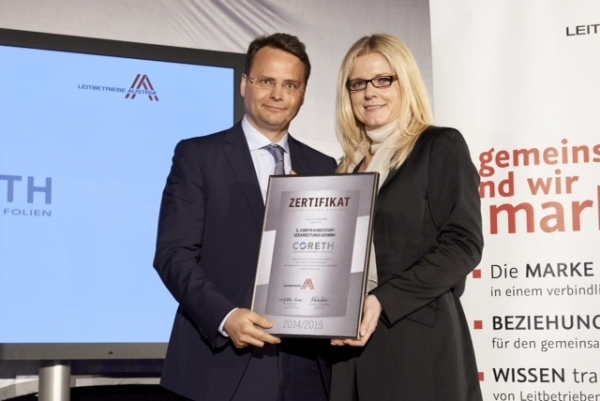
Opening of new printing hall
In December 2013 we put our new high-performance central impression flexographic printing press into operation, thus expanding our range of products and establishing an uninterrupted production chain from film production to top-quality printing!
Maximum printing width: 1,300 mm!
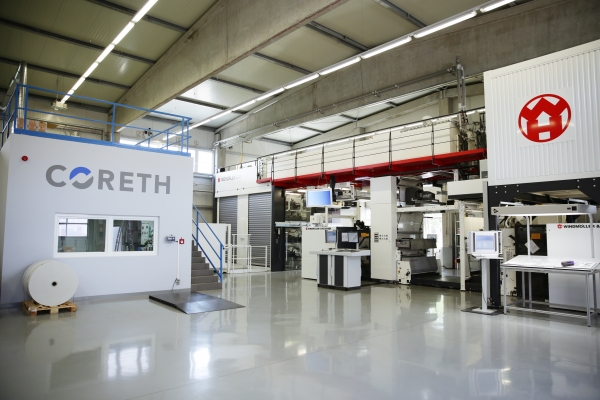
New thermal regenerative air purification system & distillation system
In our endeavour to reduce environmental impacts, we put our new thermal regenerative air purification system into operation in December 2013.
The unit burns all solvent vapors released, recovering 96 % in the form of heat.
In May 2014 we put our new distillation system into operation. Since that time all solvents have been automatically cleaned and recycled into the production process.
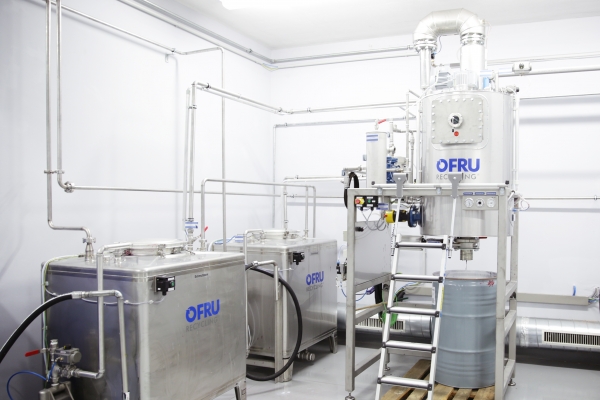
Modernization of company infrastructure
In 2013 substantial investments were made to modernize the company premises.
A new exit was established and new access roads were built; halls and storage areas were enlarged.